Quality Control Assured: Specialist Pipeline Welding Inspection Providers
Quality Control Assured: Specialist Pipeline Welding Inspection Providers
Blog Article
Comprehensive Summary of Pipeline Welding Examination Treatments
In the world of pipe building, guaranteeing the honesty and safety of bonded joints is vital. Pipeline welding examination treatments play a crucial role in guaranteeing that bonded links satisfy rigid sector criteria and specifications. From thorough pre-welding examinations to extensive post-weld assessments, a well-defined inspection procedure is vital for preserving the architectural stability of pipes. Recognizing the ins and outs of welding examination procedures is not only a governing need yet also a basic aspect of maintaining the dependability of these vital facilities.
Pre-welding Evaluation Preparations
Prior to starting the welding process, detailed pre-welding examination preparations are necessary to guarantee the stability and quality of the weld joint. These prep work include a careful evaluation of the materials to be bonded, the welding equipment, and the job environment. The materials need to be examined for any type of issues, pollutants, or disparities that could endanger the weld. This consists of checking for proper product grades, dimensions, and surface problems. Pipeline Welding Inspection. Additionally, the welding devices needs to be evaluated to verify that it remains in great working problem, calibrated properly, and appropriate for the specific welding process. Any type of concerns with the equipment must be resolved immediately to protect against flaws in the weld. The work environment must be reviewed for sanitation, proper ventilation, and safety steps to make sure a conducive setup for the welding operation. By performing extensive pre-welding inspection prep work, possible problems can be recognized and settled early, causing premium and trusted weld joints.
Welding Procedure Qualification
Thorough pre-welding assessment prep work lay the structure for the vital process of Welding Procedure Certification, guaranteeing the integrity and quality of the weld joint. Welding Treatment Qualification (WPQ) is a vital action in the welding process that entails testing and licensing welding treatments to ensure they fulfill specific requirements and requirements. The WPQ procedure usually consists of welding treatment specification growth, welding treatment certification testing, and documentation of the outcomes.
Throughout welding procedure specification advancement, vital details such as the welding procedure, welding materials, joint design, and welding parameters are defined to develop a thorough procedure. Consequently, welding procedure qualification screening is conducted to verify the proposed procedure's integrity. This screening usually entails welding examination promo codes that undergo various mechanical and non-destructive examinations to evaluate the weld's top quality and adherence to the defined standards.
In-process Weld Evaluation
Throughout the welding process, in-process weld examination plays an important duty in guaranteeing the quality and stability of the weld joint - Pipeline Welding Inspection. This type of examination includes checking the welding specifications, examining the weld bead development, and identifying any type of possible problems or gaps as they occur. By conducting in-process weld examinations, welding operators can quickly resolve any kind of issues that might develop, therefore protecting against additional issues and ensuring that the last weld fulfills the needed specifications
Common techniques made use of for in-process weld inspection include aesthetic inspection, fluid penetrant screening, magnetic bit testing, ultrasonic screening, and radiographic testing. Aesthetic inspection is often the very first step while doing so, permitting inspectors to aesthetically assess the weld for surface area abnormalities such as fractures, porosity, or insufficient fusion. A lot more innovative approaches like ultrasonic testing and radiographic screening supply in-depth understandings right into the interior structure of the Full Report weld, guaranteeing that there are no surprise flaws that can compromise the weld joint's strength and integrity. On the whole, in-process weld assessment is essential for maintaining the top quality and integrity of bonded pipes.
Non-destructive Screening (NDT)
Non-destructive Screening (NDT) is a critical method employed in pipeline welding assessment to assess the stability of weld joints without causing damage to the welded structure. By utilizing various NDT strategies, inspectors can examine the quality of welds and identify any type of defects or suspensions that may jeopardize the structural soundness of the pipeline. Typical NDT methods made use of in pipeline welding evaluation consist of Radiographic Testing (RT), Ultrasonic Testing (UT), Magnetic Fragment Testing (MPT), Liquid Penetrant Testing (LPT), and Visual Testing (VT)
RT entails using X-rays or gamma rays to produce images of the inner structure of the weld, enabling assessors to spot flaws such as porosity, splits, or insufficient blend. UT makes use of high-frequency acoustic waves to identify imperfections below the surface area of the weld, offering thorough information about the dimension and place of issues. MPT and LPT are made use of to identify surface-breaking issues by applying magnetic bits or penetrant liquids to the weld location. Furthermore, VT includes visual assessment of welds to determine any visible flaws.
Post-weld Assessment and Paperwork
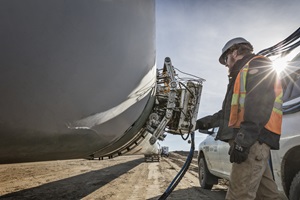
Documentation of post-weld inspection searchings for is crucial for preserving quality assurance records and making sure compliance with sector criteria and policies. Detailed reports ought to include info concerning the examination techniques made use of, the location and nature of any problems found, and any restorative actions taken - Pipeline Welding Inspection. Proper documentation not only functions as a document of the weld's top quality however additionally help in future upkeep and examination processes
Conclusion
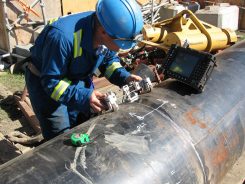
Finally, pipeline welding examination treatments play an essential role in important source ensuring the top quality and honesty of welds. From pre-welding evaluations to post-weld documents, each action is necessary in maintaining the safety and security and efficiency of pipes. By following established procedures and conducting detailed evaluations, prospective issues can be determined and dealt with prior to they result in pricey repairs or failings. In general, explanation adherence to appropriate assessment methods is crucial to the success of pipeline welding projects.
From thorough pre-welding examinations to thorough post-weld analyses, a distinct examination procedure is necessary for keeping the architectural soundness of pipelines. By performing in-process weld inspections, welding operators can promptly address any concerns that might arise, therefore making certain and protecting against further issues that the last weld satisfies the required specs.
Typical techniques utilized for in-process weld examination include aesthetic assessment, fluid penetrant screening, magnetic bit testing, ultrasonic screening, and radiographic screening.Non-destructive Screening (NDT) is a critical method employed in pipe welding inspection to assess the integrity of weld joints without creating damages to the bonded structure. Post-weld examination involves numerous methods to examine the welds for defects, including visual examination, dye penetrant screening, magnetic fragment testing, ultrasonic testing, and radiographic testing.
Report this page